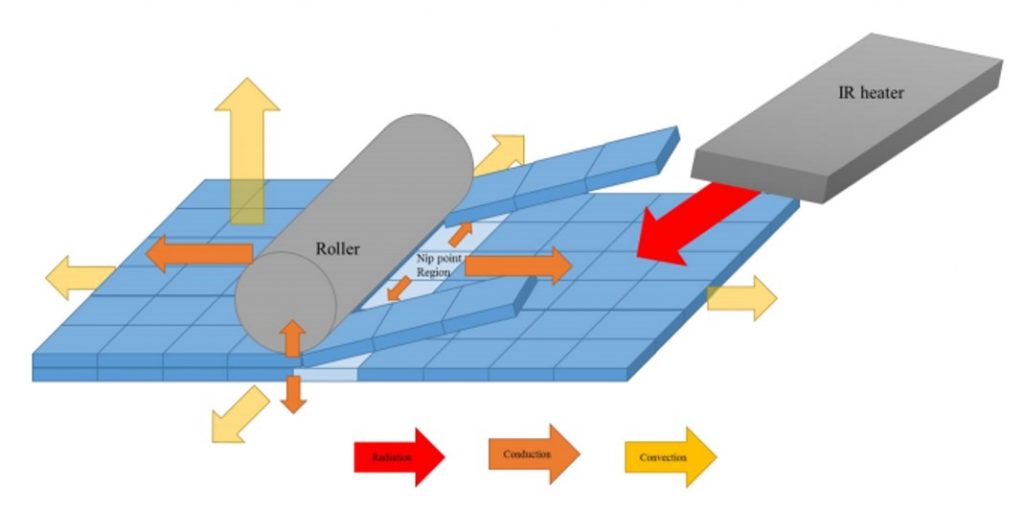
Authors
Kaishu Xia, Ramy Harik, Jeremy Herrera, Josh Patel, Brian Grimsley
Conference
SAMPE Conference & Exhibition. Long Beach, California, US.
Abstract
Material placement at the ideal nip point temperature over complex surfaces with uniformity across the width of the compaction rollers results in optimized part properties for Automated Fiber Placement (AFP) processes. However, current AFP systems utilize heat control models and methodologies, based on multiple process parameters such as feed-rate and orientation, that are mostly open-loop. Here, infrared (IR) heater input is calibrated as a function of process parameters during machine qualification. This work presents a numerical simulation to predict arrayed infrared (AIR) emitter radiation onto a substrate that includes view factor implementation, IR radiative heat flow calculation, energy rate balance, and a transient heat transfer model. The purpose of this numerical model is to predict nip point temperature on complex surfaces, serving as a baseline for a new arrayed-infrared (AIR) thermoset heater to improve AFP process control.
It is anticipated that this simulation will accurately control the temperature for high-speed AFP layup of complex geometries. An anticipated result of an AIR heater system is that material calibration and testing will be reduced as temperature is instantaneously monitored and controlled.
Therefore, temperature across the roller width will be uniform during placement of complex parts, independent of their geometry.
Citation
Kaishu Xia, Ramy Harik, Jeremy Herrera, Josh Patel, & Brian Grimsley. (May 2018). Numerical Simulation of AFP Nip Point Temperature Prediction for Complex Geometries. SAMPE Conference & Exhibition. Long Beach, California, US.
Link: https://ntrs.nasa.gov/search.jsp?R=20200002530
Documents